¿Qué se debe sentir cuando alguien acaba de cerrar la compra de un automóvil que vale más de 2,4 millones de euros? Buena pregunta. El proceso de adquisición y fabricación de un Bugatti Chiron no tiene nada que ver, ni mucho menos, con el proceso de compra de cualquier otro automóvil. En las fábricas de Bugatti no hay robots, no hay cadenas de montaje con sistemas de transporte de los vehículos en el ensamblado. Todo lo que veremos mientras se fabrica el Bugatti Chiron será un suelo de material plástico brillante e inmaculado, sin una gota de aceite. Y es que para Bugatti su factoría no es una fábrica al uso. De hecho desde la marca se refieren a ella como el Bugatti Atelier, rescatando el vocablo atelier, taller en francés. Y he aquí 10 curiosidades que probablemente desconocías del Bugatti Chiron y su proceso de compra y fabricación.
1. Mientras lees estas líneas, Bugatti está ensamblando 12 unidades del Bugatti Chiron. Los primeros Bugatti Chiron en llegar a sus orgullosos clientes se entregarán antes de abril. En 2017 se fabricarán un total de 70 unidades del Bugatti Chiron, unas cifras realmente modestas si lo comparamos con cualquier otra fábrica de coches, en los que su producción anual se cifra en decenas y cientos de miles de unidades.
2. La fabricación de un Bugatti Chiron, desde que comienza su ensamblado, hasta que se entrega, dura nada más y nada menos que seis meses. Desde que el cliente procede a la configuración de su coche, hasta la entrega, el proceso suele prolongarse unos nueve meses. Un embarazo.
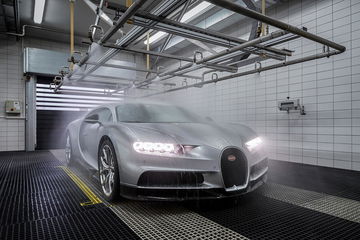
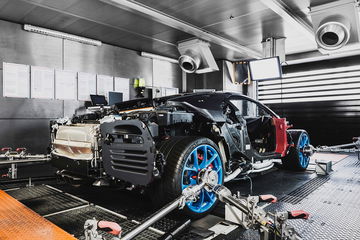
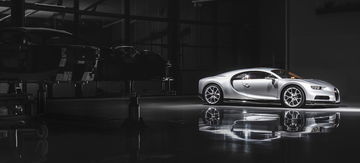
3.Cada Bugatti Chiron requiere el ensamblado, de manera completamente manual, de 1.800 piezas individuales. Imagínatelo como un inmenso Lego de 1.500 CV de potencia y 2,4 millones de euros. En la fábrica de Molsheim en la que se ensambla el Bugatti Chiron trabajan 20 empleados de la marca, únicamente en el proceso de ensamblado.
4. El proceso de fabricación de Bugatti Chiron comienza mucho antes, incluso, del ensamblado de las primeras piezas, comienza en el proceso de configuración del vehículo. El cliente se reúne personalmente con el propio diseñador del Bugatti Chiron para configurar su máquina. El cliente tiene ante sí 23 tonos de carrocería sólidos y otros 8 tonos de fibra de carbono barnizada y teñida. También puede escoger entre 31 tonos de piel y otros 8 de Alcantara, así como 30 tonos para las costuras, 18 para las alfombrillas y otros 11 tonos para el cinturón de seguridad. En cualquier caso, y dado que la personalización es máxima, el cliente puede salirse de la paleta de colores inicial y escoger entre miles de tonalidades diferentes.
5. La máxima personalización posible. Bugatti asegura que el cliente puede reservar un Chiron con un acabado de pintura que vaya a juego con su bolso. Y si lo dicen es porque apostamos que algún cliente habrá llegado a solicitar tal cosa. También puede incorporar sus iniciales en los revestimientos interiores, en los reposacabezas o incluso en el alerón retráctil trasero. Bugatti ha dispuesto de una sección específica para atender las necesidades más exquisitas de sus clientes, La Maison Pur Sang.
6. Un mes antes de que se inicie el proceso de ensamblado propiamente dicho, Bugatti comienza a dar forma al monocasco del Bugatti Chiron. El proceso de pintura, y de la aplicación de las diferentes capas, se prolonga durante nada más y nada menos que tres semanas. Los acabados de pintura de fibra de carbono visible y teñida requieren seis capas, y hasta ocho capas si se escogen acabados especiales, metalizados, o perlados. Todo el proceso de pintura es completamente manual.
7. En la fábrica del Bugatti Chiron no existen robots, ni lineas de montaje mecanizadas. El proceso de una fábrica como la de Bugatti es más parecido al de un taller de Fórmula 1, que al de cualquier otra fábrica de turismos del mundo. El ensamblado se lleva a cabo en 12 estaciones de trabajo independientes, comenzando por la primera, en la que se acondiciona el motor, que ya ha sido ensamblado previamente en la fábrica del Grupo Volkswagen en Salzgitter. En la segunda estación se ensambla el motor sobre el chasis, un motor que pesa nada más y nada menos que 628 kilogramos.
8. Uno de los procesos más importantes del ensamblado es lo que Bugatti denomina como el matrimonio, la unión de la sección trasera con el monocasco. Las dos piezas más grandes y pesadas del Bugatti Chiron se unen con tan solo 14 tornillos. 14 tornillos que Bugatti decidió que fueran de titanio, por ser muy ligeros (cada uno solo pesa 34 gramos) y resistentes. Un Bugatti Chiron tiene un total de 1.800 uniones, cada una de las cuales requiere un atornillado con una presión concreta. Hasta aquí ninguna sorpresa. Eso mismo sucede en el proceso de fabricación de cualquier otro coche. Lo peculiar del Bugatti Chiron es que existe un proceso de documentación en el que se registra el par aplicado por el sistema de atornillado, y el operario que lo realizó, en un total de 1.068 uniones.
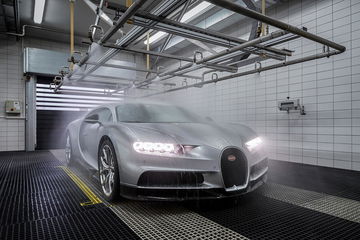
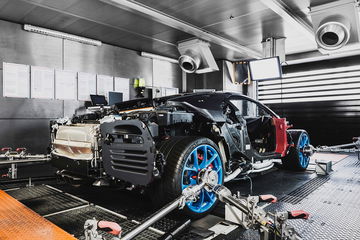
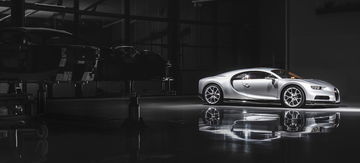
9. Tras el ensamblado final, Bugatti pone a prueba a cada Chiron en el banco de rodillos más potente del mundo. Suficientemente potente como para trabajar con un Bugatti Chiron de 1.500 CV a pleno rendimiento y simulando velocidades superiores a los 200 km/h. Estas pruebas se prolongan hasta tres horas y en ellas el vehículo recorre un total de 60 kilómetros. Bugatti prueba incluso la estanqueidad de cada coche en un túnel meteorológico en el que se simulan las condiciones más adversas, con intensidades dignas de la lluvia de un monzón, para asegurarse de que no hay fugas.
10. El proceso de calidad y pruebas es tan importante para Bugatti, para garantizar que sus clientes reciben un hiperdeportivo con todas las garantías posibles, que más allá de las pruebas en banco de rodillos, y en el túnel meteorológico, Bugatti realiza una prueba en condiciones reales que se prolonga durante más de 300 kilómetros. En estas pruebas, realizadas en carretera abierta y pista cerrada, el Bugatti Chiron supera los 250 km/h. Bugatti se preocupa, incluso, de que las pruebas se realicen con una protección de bajos y unas ruedas diferentes a las que se entregarán finalmente, para evitar desperfectos. Tras estas pruebas se remplaza, incluso, el aceite de la transmisión.
En Diariomotor:
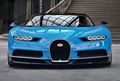
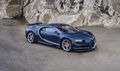